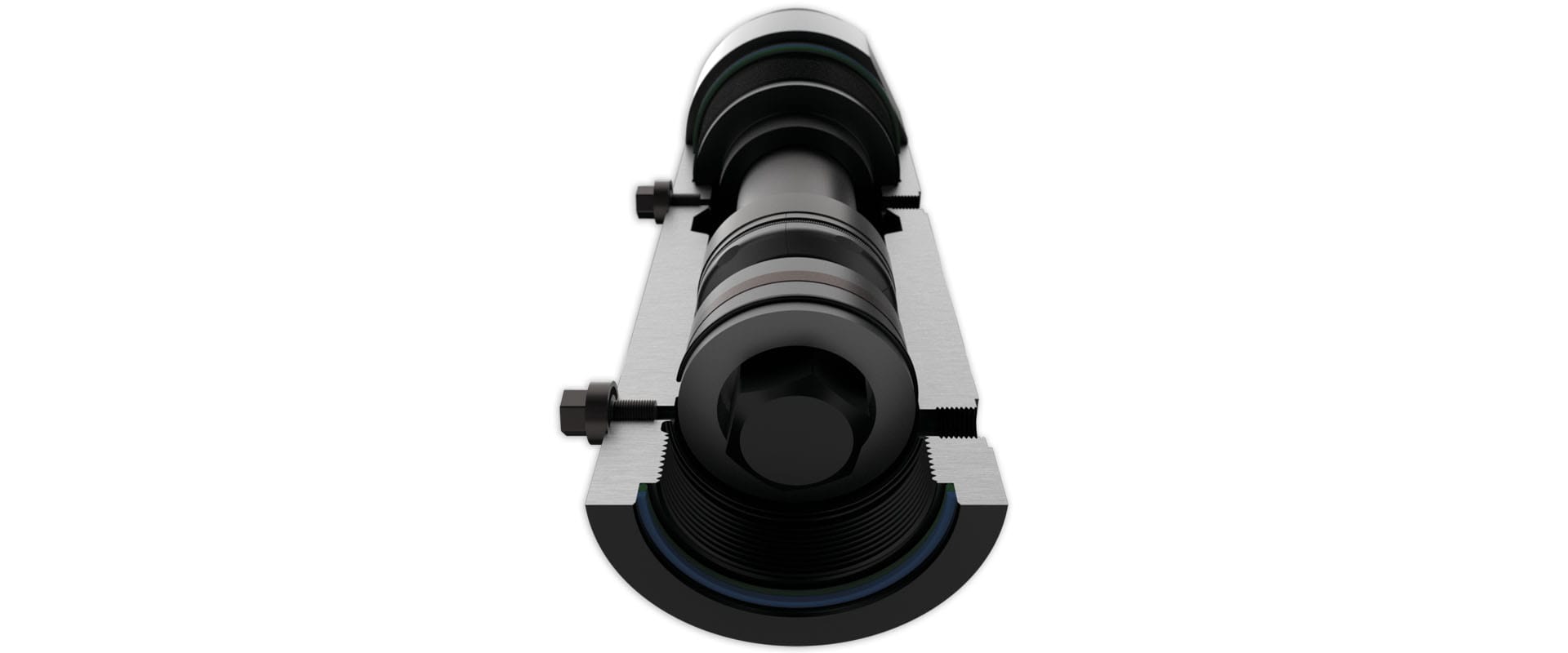
Many components in the world of plastic molding rely on hydraulic power, because it normally allows much greater pressure (and therefore force) than other solutions, such as pneumatic. In fact, a hydraulic cylinder with a 50 mm bore, working at a pressure of 200 bars, will build a force of 3926 daN while pushing; this means that it could hold up (statically) more than 4 tons applied directly down towards its rod.
But in plastic injection and die casting, sometimes you need more than that. For example, in the case of motion on the fixed part of the mold, you may need to make sure it stays mechanically locked in that position, so that the finished piece will take the desired shape and not have burs.
Our self-locking system solves these issues.
Self-Locking Hydraulic Cylinder
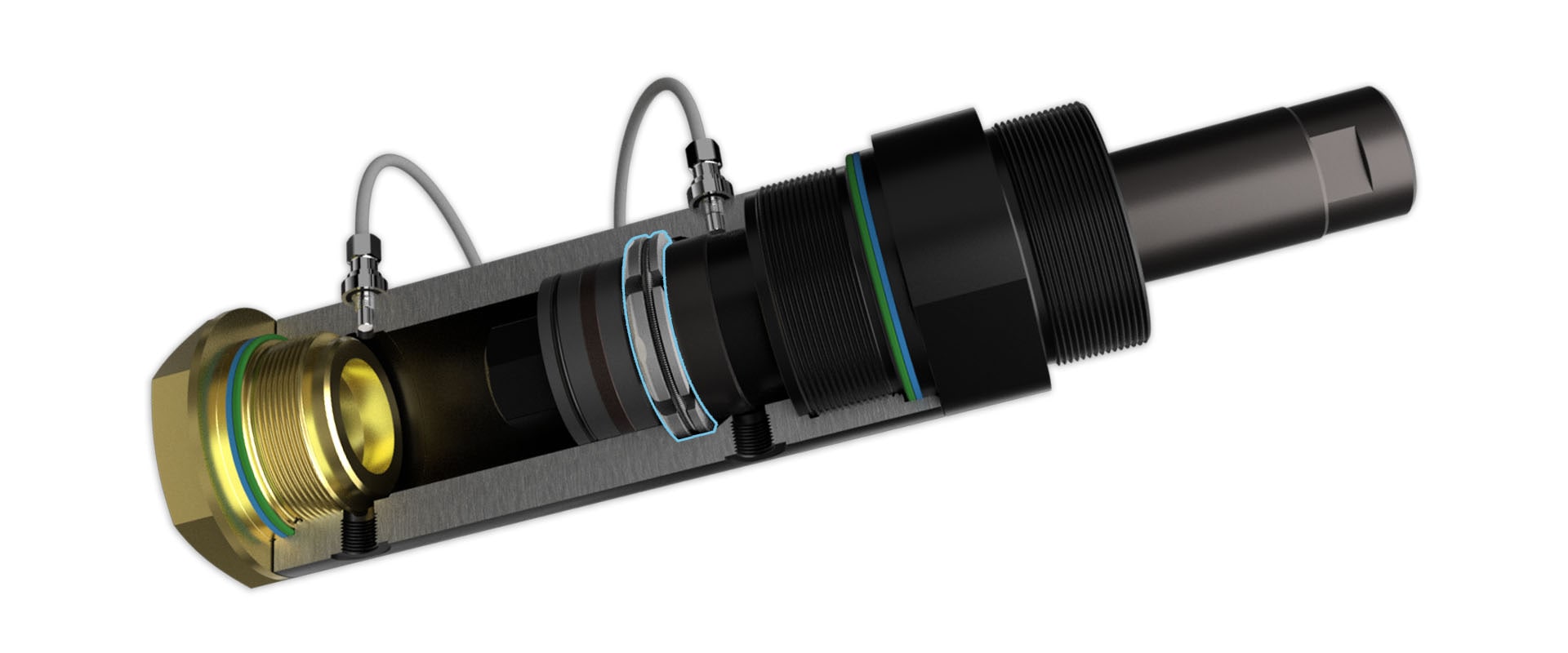
Let’s compare a standard hydraulic cylinder to a cylinder with our self-locking technology. With a comparable bore of 45 mm, instead of holding 4 tons, it will withstand 5x more (20 tons) with an extended rod, with virtually no need to maintain pressure. So how does it work?
How the Self-Locking Hydraulic Cylinder works
The rod-piston group is composed of a floating piston and high-resistance floating sectors. When the rod-extended motion begins, the sectors stay closed until they meet with a groove machined on the inside of the body.
At this point, the cone-section shaped piston will expand the sectors, which will fill up the space between the piston and the body, firmly locking it in the rod-extended position.
Any force vector coming from the molded material will be relieved through the sectors and along the reinforced body, thanks to the accurately engineered angles among the components.
Everything can be kept in place with a minimum pressure inside of the chamber.
When it’s time to unlock the cylinder, the oil getting inside of the cylidner pushes the piston downwards, giving room for the sectors to collapse back to their original position. The rod will then be free to retract, completing the cycle.
Pre-Loading Flange
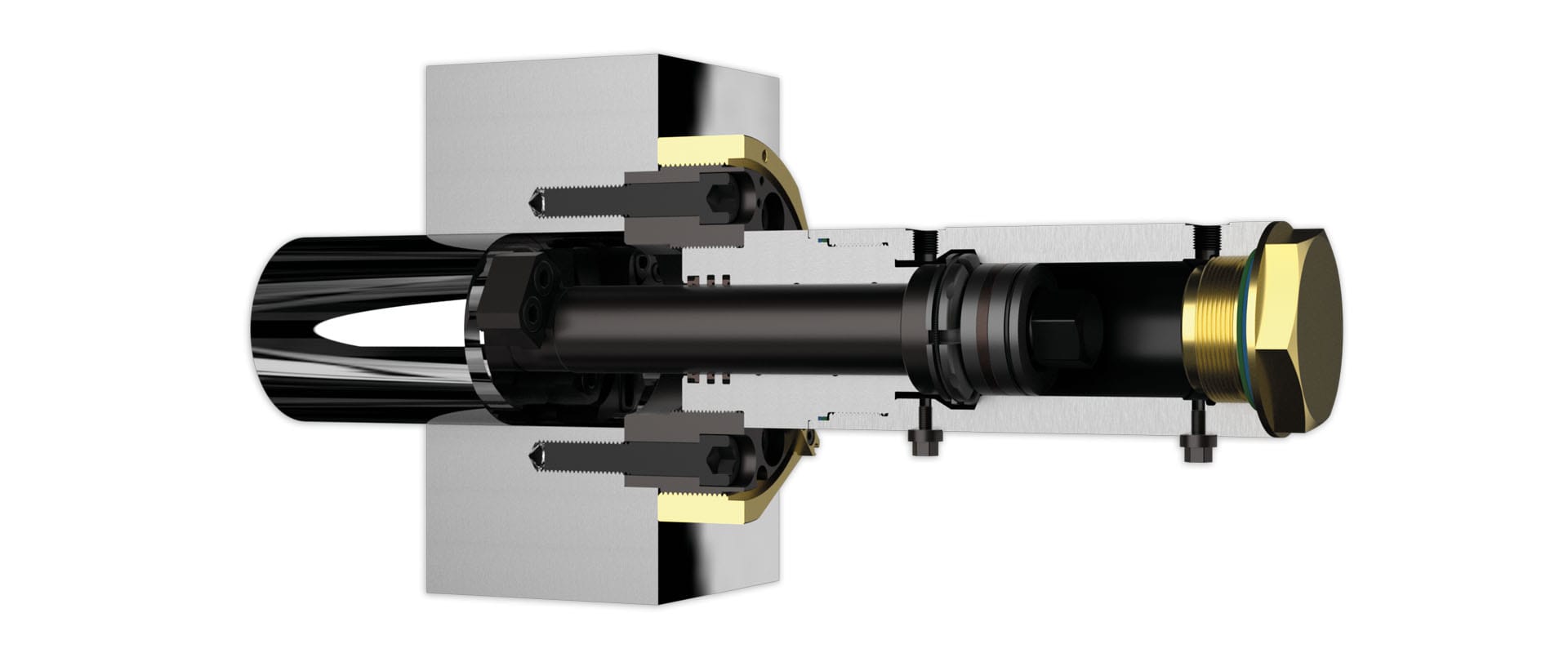
The above mentioned mechanical locking paves the way for another interesting technology: pre-loading. How can it help improve the quality of your molding?
When plastic is injected, it creates a certain amount of pressure (and force) all around the plug. Due to the fact that fluids such as oil are actually compressible, the plug will give up just that tiny amount of space, and plastic will sap between it and the rest of the mold. Together with small, accumulated tolerances among all the pieces of the moving part, this results in burs on the finished piece, that either need to be removed manually, or are left there, reducing the overall quality of the product.
The ability for the self-locking mechanism to withstand great forces at the end of the stroke can be used to pre-load the rod. With our special pre-loading flange, your operator can tighten the external ring during set-up, compressing the rod and the parts that are linked to it. This locks the plug in place and makes it able to withstand injection pressure, which in turn will give you a molded part without imperfections.