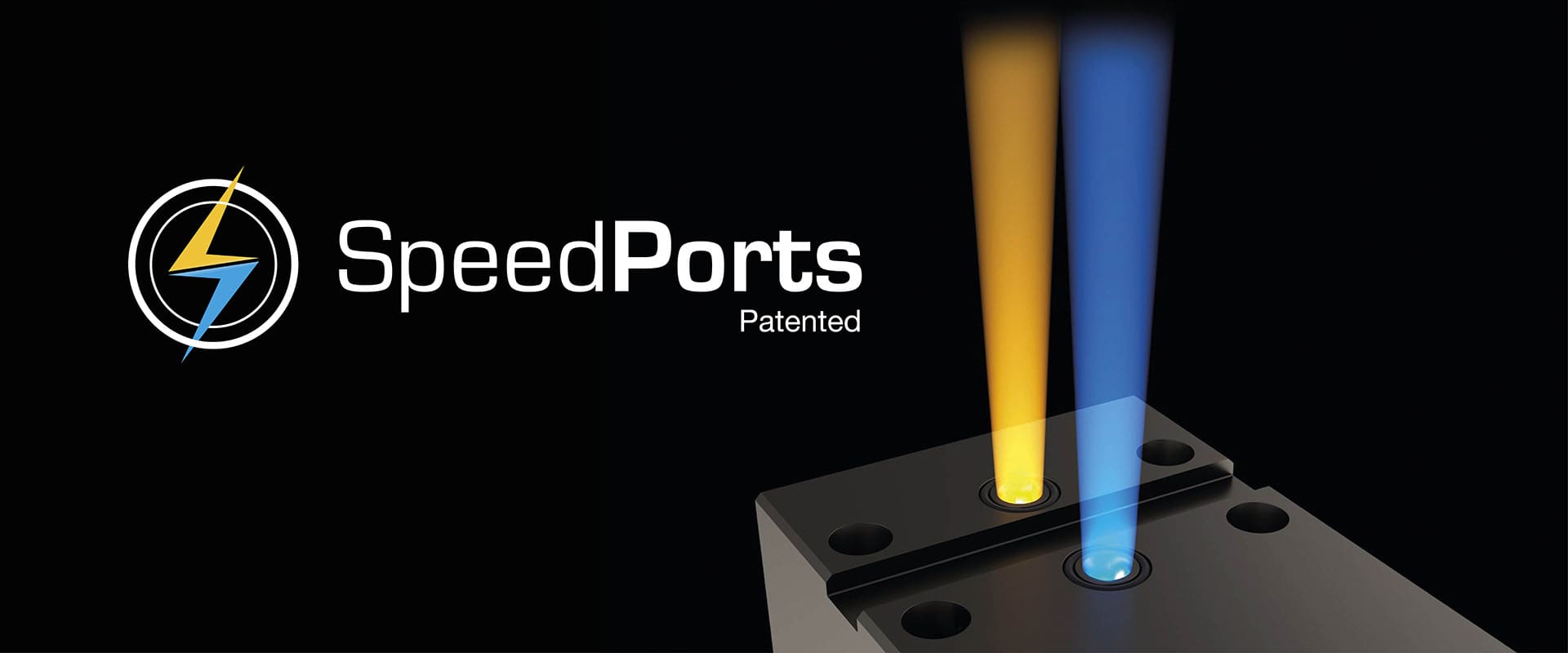
Speed is the vital point of every cylinder, and increasing it means everything to the molder. It allows to cut costs, save time and bypass barriers. Efficiency is what matters, everything else is boredom. For cylinders, efficiency is SpeedPorts.
The constant focus of talented engineers is always towards breaking the limits, and humble minds strive to always put themselves under discussion. Then, sometimes, comes that spark which opens the way to innovation. Our R&D department has always followed this line of thought, and after countless support calls, meetings with our customers and deep analysis and testing, has developed an astounding, patent-pending solution.
High Speed Delivery for Hydraulic Cylinders
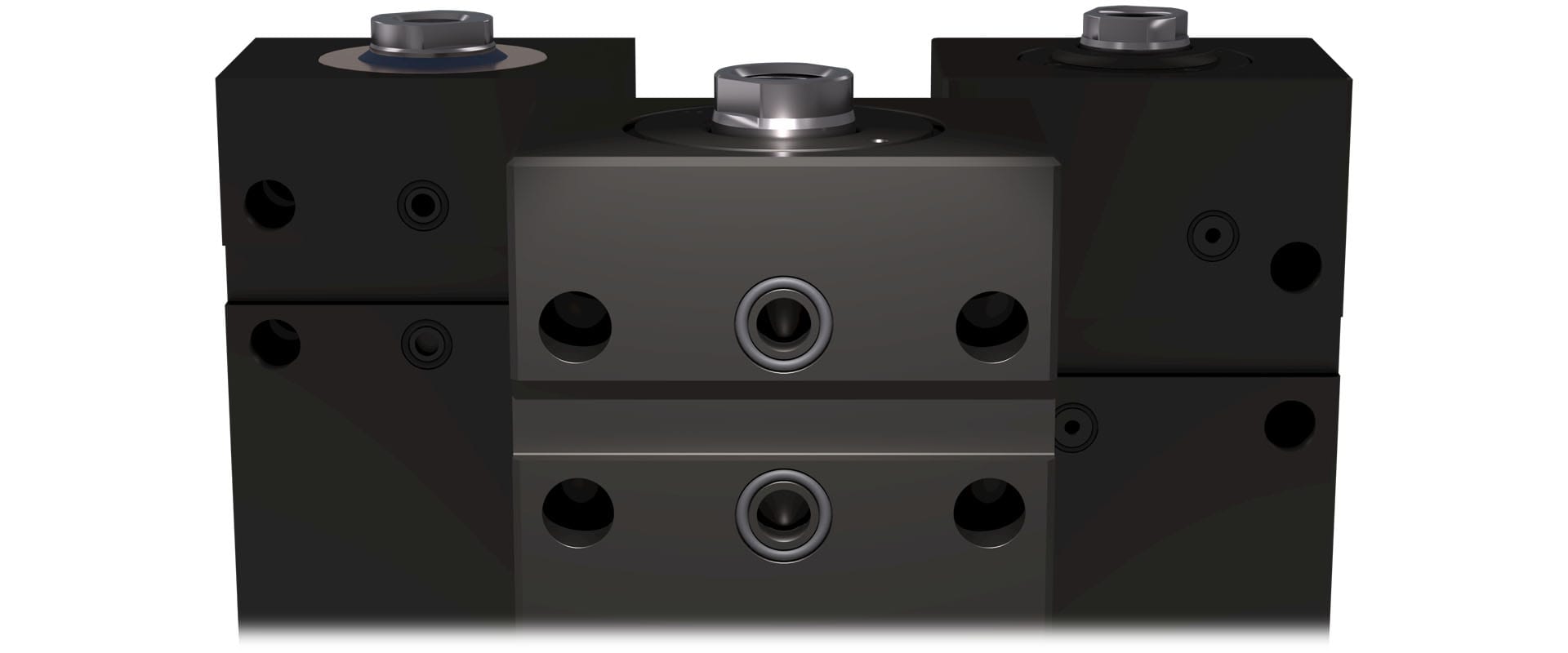
SpeedPorts allows to double the oil flow on any O-Ring delivery, while keeping the dimensions unchanged. Therefore, there is potentially no performance difference between a SpeedPorts oil delivery and a typical threaded oil delivery; compromises are a thing of the past. Now you can choose having an extremely compact cylinder with the same speed as a much bigger one.
Pressure Loss vs. Speed (Lower is Better)
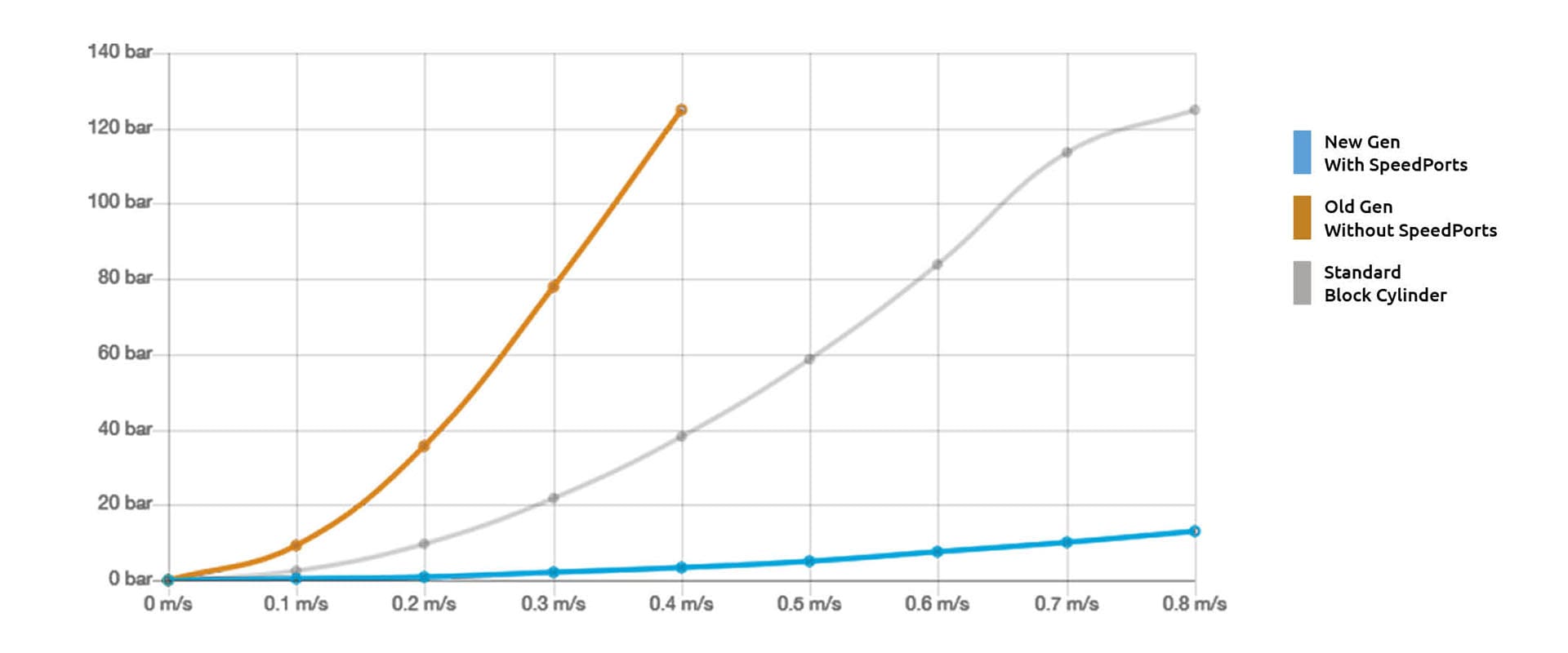
Let’s have a look at raw numbers to understand how SpeedPorts can change your work for the better. Our example setup will be an ejection plate moved by four typical block cylinders, bore 80, stroke 200 mm. In most cases, hydraulic circuits are kept to a pressure of 100÷120 bar to grant an efficient and constant delivery, so we’ll base our calculation around this value.
A standard compact cylinder of that size offers an O-Ring port with a diameter of either 6 or 8 mm. Even in the best case, at a typical speed of 0.3 m/s, this cylinder will have a load loss of ~20 bar. So we have:
Pump Load - Port Loss - Friction Loss - Overall Circuit Loss = Load Left
120 bar - 20 bar - ~10 bar - ~15 bar = 75 bar
Basically, on a decent-performing hydraulic pump, we have already lost one third of the load, and O-Ring port losses had a good part in it. On the other hand, a SpeedPorts cylinder, with a diameter of 14mm at the port and the same speed of 0.3 m/s, will suffer a load loss of less than 2 bar. Let’s redo the math:
120 bar - 2 bar - ~10 bar - ~15 bar = ~93 bar
The outcome is a little better. In this case, if the rest of the circuit is well-dimensioned, the load drop will be negligible. Now, let’s up the stakes. How about we want our cylinder to go up to 0.8 m/s? In this case, a standard block cylinder will have a load loss of ~125 bar. Therefore:
120 bar - 125 bar - ~10 bar - ~15 bar = ~-30 bar
We're trying to defy the laws of physics here. This means that the oil pump will have to be set to at least 160 bar to even have a chance to work at this speed. Instead, a SpeedPorts cylinder, on the same setup, will keep a speed of 0.8 m/s and bring a loss of only about 12 bar.
120 bar - 12 bar - ~10 bar - ~15 bar = ~83 bar
Much better. At a speed which is practically three times our first calculation, the load drop is even less! This means that on average, cylinders using the SpeedPorts technology can go two to three times as fast as comparable products and cycle times for the circuit could drop of a good 10%, leading to huge savings in the long run.