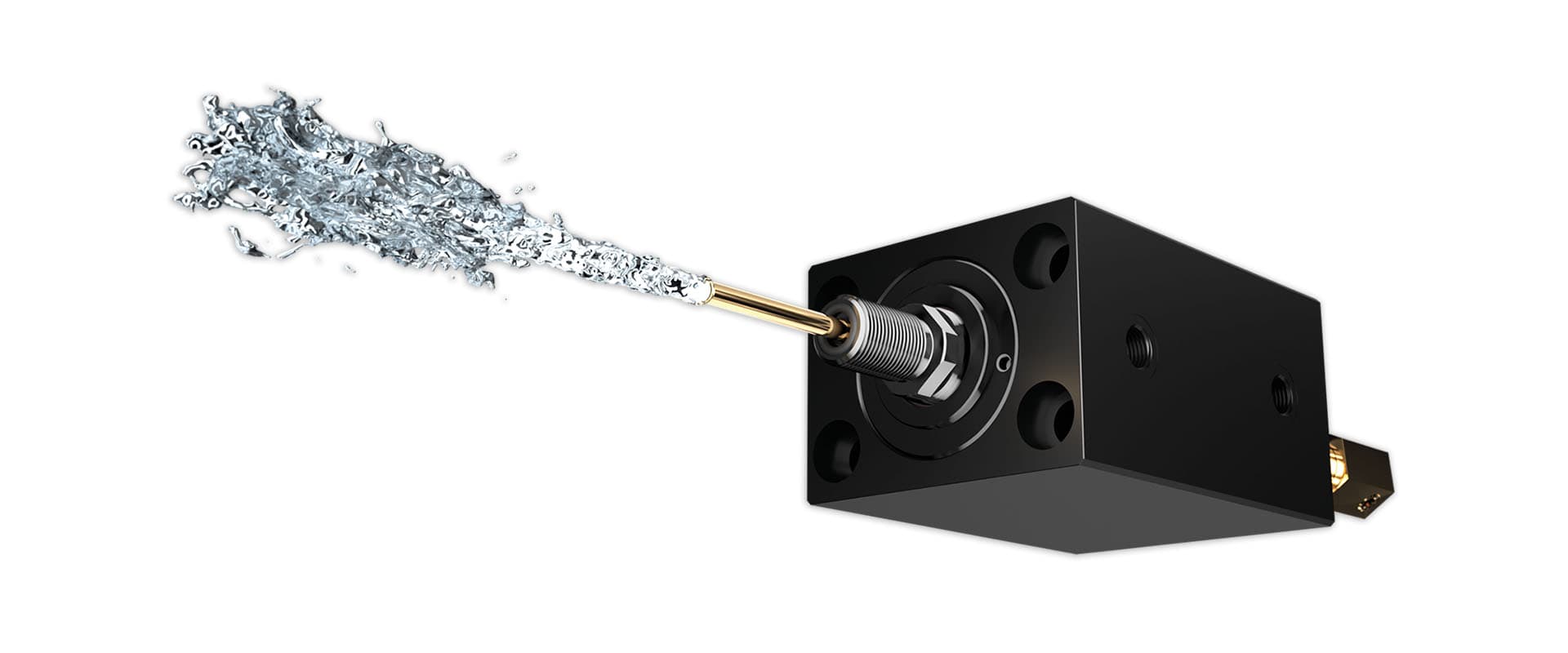
Temperature is always a hot topic among molders and mold makers. On plastic molds, and even more so on die casting or low-pressure aluminum molds, high temperatures are needed to reach the target material fluidity and therefore achieve a good finished product. On the other hand, this brings a toll on various components, such as seals.
In the case of hydraulic cylinders, the reduced lifespan of their seals force molders to halt their production in order to change them, losing precious time and, therefore, money. These issues were the motivation behind the development of our exclusive cooling systems.
Hydraulikzylinder mit Kolbenstagen-Kühlung
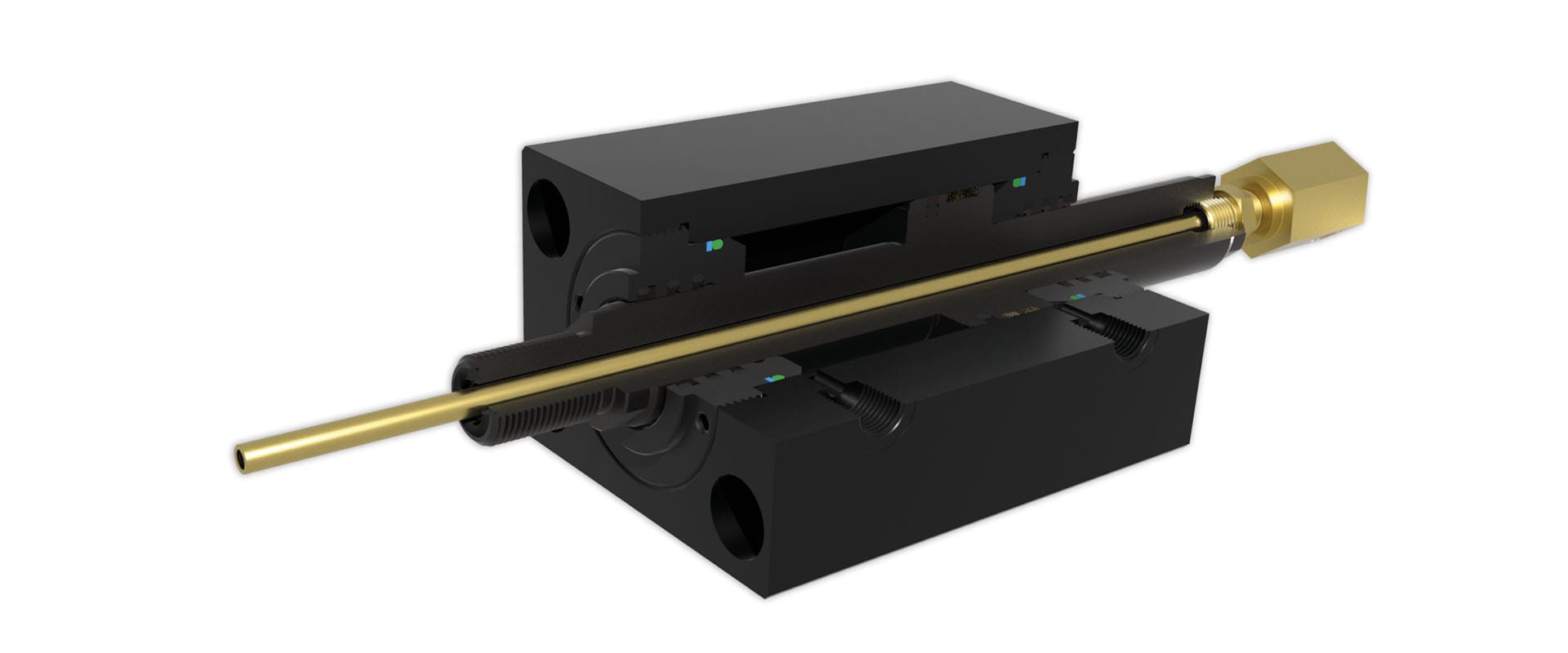
The first solution is a cooling circuit applied to a pass-through rod, which is drilled along its whole length. This circuit plugs to either a mineral-based fluid or a water-glycol source, so that the cooling fluid will not only cool the rod and piston seals, but can also be used to extend the cooling circuit to the connected pin or cart. The advantages are clear:
- Longer seals lifespan. Since all the most important seals are in contact with the rod (and it is the rod itself that propagates heat from the mold to the rest of the cylinder), cooling this component will greatly help with their performance and efficiency, reducing maintenance downtime.
- Cooling circuit extends to the mold. If you had the (mis)adventure of designing or working on a mold with strict cooling requirements, you know it can get messy rather quickly, with all those pipes running everywhere, trying to reduce temperatures where it matters. With our integrated rod cooling, the circuit doesn't stop at the rod, but it can be extended to what ever part of the mold that is connected to the cylinder: plugs, carts, you name it. Design complexity (and the accompanying maintenance nightmare) will be greatly reduced by using an integrated and much more compact system, which translates to lower running costs.
Hydraulikzylinder mit Gehäuse-Kühlung
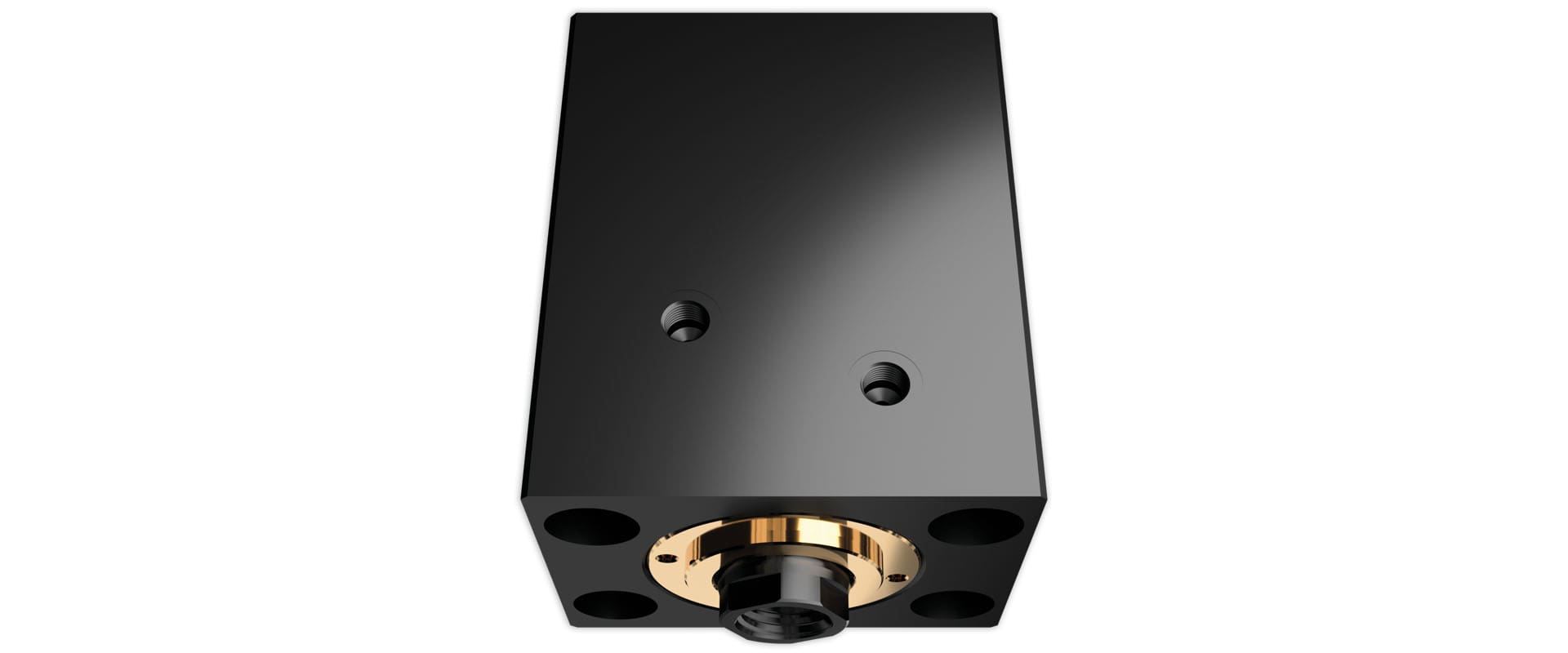
The second solution is as compact as it gets: a separate cooling circuit is built inside of the body of the cylinder. The coolant is routed all around the cartridge, protecting the seals from reaching high temperatures.
By not having external components, the system can be extremely compact and it can even take advantage of the same mineral-based fluid or water-glycol circuit that is used for cylinder movement. This system is compact, but still extremely efficient: it can bring a drop of about 50° C compared to the original running temperature!
The improvements brought with this solution towards better maintenance and efficiency are breathtaking. Instead of a more theoretical explaination, we’let the result of a real case application speak.
One of our first customers for this kind of product had a few cylinders inside of the fixed part of a die-casting mold, for a squeeze-casting procedure.
Due to the high temperatures reached, it was needed to halt production, open the cylinders, replace the seals and put the cylinders back in place every 10 days.
Since they implemented our cartridge-cooled cylinders, this maintenance interval has been extended to 8 months!
This is just a small example of the kind of saving that a cooled cylinder can bring in the long run.
Watch a V450 CP cylinder go from 190° C to 75° C in 17 seconds.